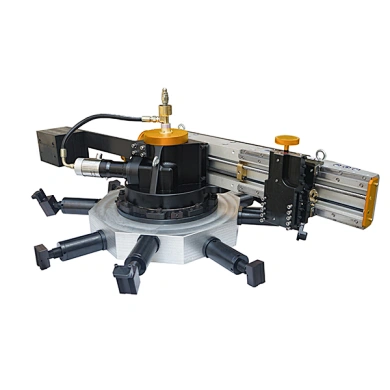
。
# Flange Preparation Machine for Chemical Plant Maintenance
## The Importance of Flange Preparation in Chemical Plants
Flange preparation is a critical aspect of chemical plant maintenance that ensures the integrity and safety of piping systems. Properly prepared flanges create leak-proof connections that can withstand the harsh conditions found in chemical processing environments. Inadequate flange preparation can lead to dangerous leaks, costly downtime, and potential environmental hazards.
## What is a Flange Preparation Machine?
A flange preparation machine is a specialized tool designed to efficiently and precisely prepare flange faces for optimal sealing. These machines typically perform several key functions:
– Surface cleaning and degreasing
– Removal of old gasket material
– Restoration of proper surface finish
– Alignment correction
– Beveling and edge preparation
## Key Features of Modern Flange Preparation Machines
Today’s advanced flange preparation machines offer numerous features that make them indispensable for chemical plant maintenance:
### 1. Portability and Versatility
Modern machines are designed to be portable, allowing technicians to bring the equipment directly to the flange location rather than removing piping sections. This significantly reduces downtime during maintenance operations.
### 2. Precision Machining Capabilities
High-quality machines can achieve surface finishes that meet or exceed industry standards (typically Ra 125-250 µin for most chemical applications). Some models feature digital readouts for precise depth control.
### 3. Safety Features
Given the hazardous environments in chemical plants, these machines often include:
– Explosion-proof motors
– Spark-resistant materials
– Integrated dust collection systems
– Emergency stop mechanisms
## Benefits of Using Flange Preparation Machines
Implementing proper flange preparation equipment in your chemical plant maintenance program offers numerous advantages:
– Reduced downtime during maintenance operations
– Improved seal integrity and reduced leakage incidents
– Extended gasket and flange life
– Consistent preparation quality across all connections
– Lower overall maintenance costs
– Enhanced worker safety
## Choosing the Right Flange Preparation Machine
When selecting equipment for your chemical plant, consider these factors:
### 1. Flange Size Range
Ensure the machine can handle the full range of flange sizes in your facility, from small instrument connections to large process piping.
### 2. Material Compatibility
The machine must be capable of working with all flange materials used in your plant, including carbon steel, stainless steel, and exotic alloys.
### 3. Environmental Conditions
Consider the specific environmental challenges of your facility, such as:
– Presence of flammable vapors
– Corrosive atmospheres
– Space constraints
– Accessibility issues
### 4. Ease of Use and Training Requirements
Look for machines with intuitive operation to minimize training time and reduce the potential for operator error.
## Maintenance Best Practices for Flange Preparation Machines
To ensure optimal performance and longevity of your equipment:
– Follow manufacturer’s lubrication schedules
– Regularly inspect cutting tools for wear
– Clean the machine after each use
– Store in a dry, protected environment
– Calibrate measurement systems periodically
– Train operators on proper usage techniques
## The Future of Flange Preparation Technology
Emerging trends in flange preparation include:
– Automated systems with robotic assistance
– Integrated quality control sensors
– Wireless data logging for maintenance records
– Advanced materials for longer tool life
– AI-assisted diagnostic capabilities
By investing in proper flange preparation equipment and following best practices, chemical plants can significantly improve their maintenance operations, reduce risks, and enhance overall operational efficiency.
No Responses